Greetings,
This is a 3-axis CNC machine I assembled from a kit. It cuts sheets of foam, wood, plastic, etc. from g-code files you generate from a SketchUp model. It turns a virtual model into a solid real item. I'm going to start construction of my CarBEN EV electric car.
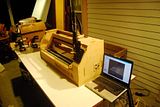
Video of test run:
http://www.youtube.com/watch?v=LCxENFw129E
First running of a test file (and the cutting bit is not powered up) -- you can see the yellow cone pointer showing the position of the cutter bit relative to the virtual sheet on the laptop screen; while the 3 stepper motors are putting the PhlatPrinter III through its paces, as it were.
Very cool machine -- I need to come up to speed on how to generate my own g-code files to get started constructing my CarBEN EV full sized working prototype electric car!
Here's a screen capture of my initial try at laying out the 2'x8' sheet of foam in DataCAD:
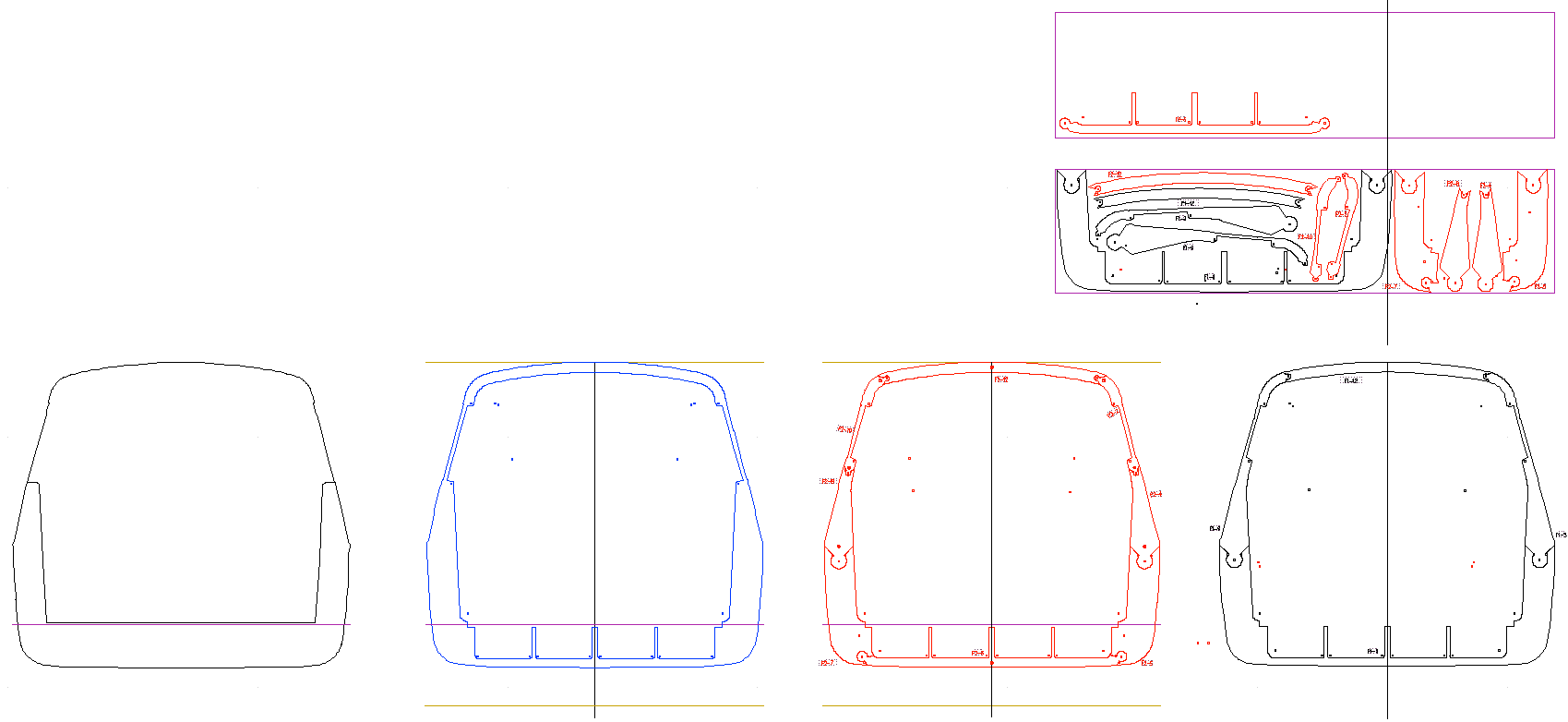
In the upper right is an approximate layout of the first 2" thick foam sheet, to be cut on on my PhlatPrinter III. I need to redo it with an alignment "rod" in the SketchUp model, that will appear as 1/2" circles, like those shown on the red F2 section. I'll use dowels to align the sections as I glue them together.
I need to confirm the limits of the cutting area -- I think the righthand edge needs a 4" band (on the 2' side) so that the X-axis friction rollers can keep hold of the sheet? And that means the F2-5 red piece will need to be moved up to the second 2'x8' foam sheet.
I also need to separate the doors, hood, wheel skirts, etc. so they can be made as pieces, and I'll have to design hinges for all of them.
This is a 3-axis CNC machine I assembled from a kit. It cuts sheets of foam, wood, plastic, etc. from g-code files you generate from a SketchUp model. It turns a virtual model into a solid real item. I'm going to start construction of my CarBEN EV electric car.
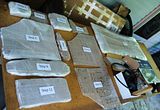
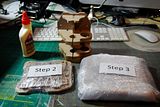
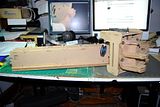
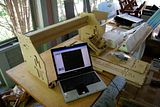
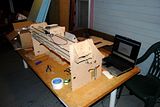
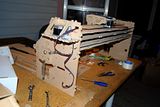
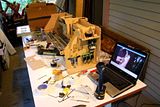
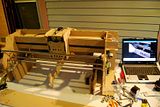


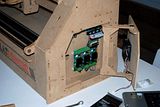
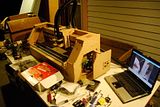
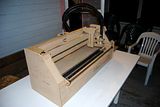
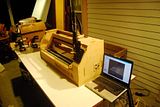
Video of test run:
http://www.youtube.com/watch?v=LCxENFw129E
First running of a test file (and the cutting bit is not powered up) -- you can see the yellow cone pointer showing the position of the cutter bit relative to the virtual sheet on the laptop screen; while the 3 stepper motors are putting the PhlatPrinter III through its paces, as it were.
Very cool machine -- I need to come up to speed on how to generate my own g-code files to get started constructing my CarBEN EV full sized working prototype electric car!
Here's a screen capture of my initial try at laying out the 2'x8' sheet of foam in DataCAD:
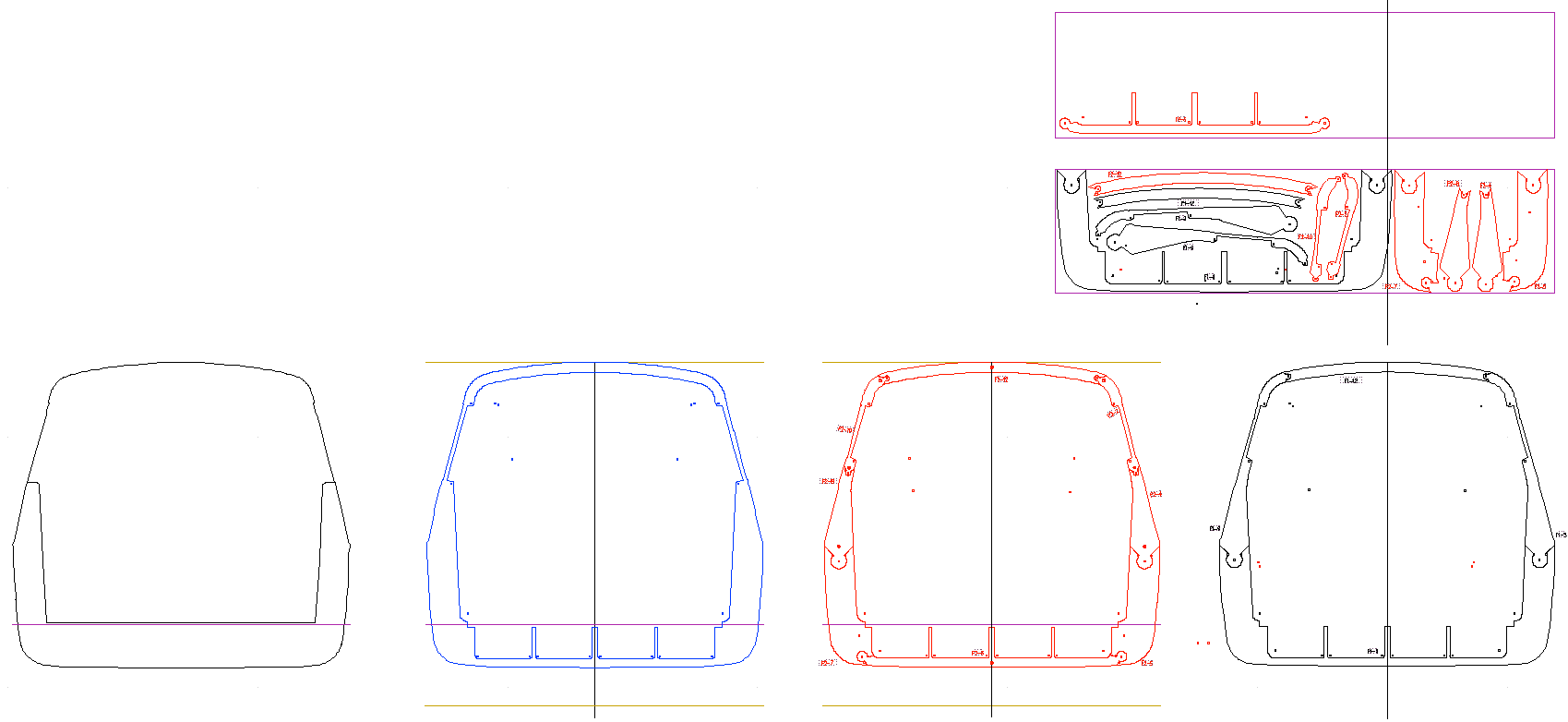
In the upper right is an approximate layout of the first 2" thick foam sheet, to be cut on on my PhlatPrinter III. I need to redo it with an alignment "rod" in the SketchUp model, that will appear as 1/2" circles, like those shown on the red F2 section. I'll use dowels to align the sections as I glue them together.
I need to confirm the limits of the cutting area -- I think the righthand edge needs a 4" band (on the 2' side) so that the X-axis friction rollers can keep hold of the sheet? And that means the F2-5 red piece will need to be moved up to the second 2'x8' foam sheet.
I also need to separate the doors, hood, wheel skirts, etc. so they can be made as pieces, and I'll have to design hinges for all of them.
Last edited by Neil Blanchard on Wed Jan 04, 2012 8:13 am, edited 1 time in total.